Would you like to streamline and automate tasks? Are you convinced that Industry 4.0 is the future, but you're not sure how to best leverage it?
If so, you're not alone! It's hard to get a grasp on how to effectively digitalize your business. What do you do? Most sheet metalworking companies usually rely on consultants to get clarity on these topics.
However, there are a few important pitfalls to avoid before you start your project and hire a consultant in your business to ensure you're getting the results you want and that will last for the future.
This article will guide you on avoiding common mistakes when automating your factory, allowing you to sit back and relax while your company operates seamlessly.
In summary
1. Ensure you find true Industry 4.0 solutions, not legacy hardware and software. If you don't get this right, you'll have trouble integrating the factory.
2. Adjust your business model to cater to the new 21st-century customer who values speed and connectivity, to reap the benefits of digital transformation.
3. Any successful digital transformation will require letting go of old software solutions. Don't be deterred by sunk costs being part of the equation.
4. Prioritize a strategic IT design; otherwise, data will be challenging to manage, and you won't be able to leverage the latest Cloud Data technologies.
5. Don't neglect IT security risks. Ensure your network is always secure, and your operating system is up-to-date.
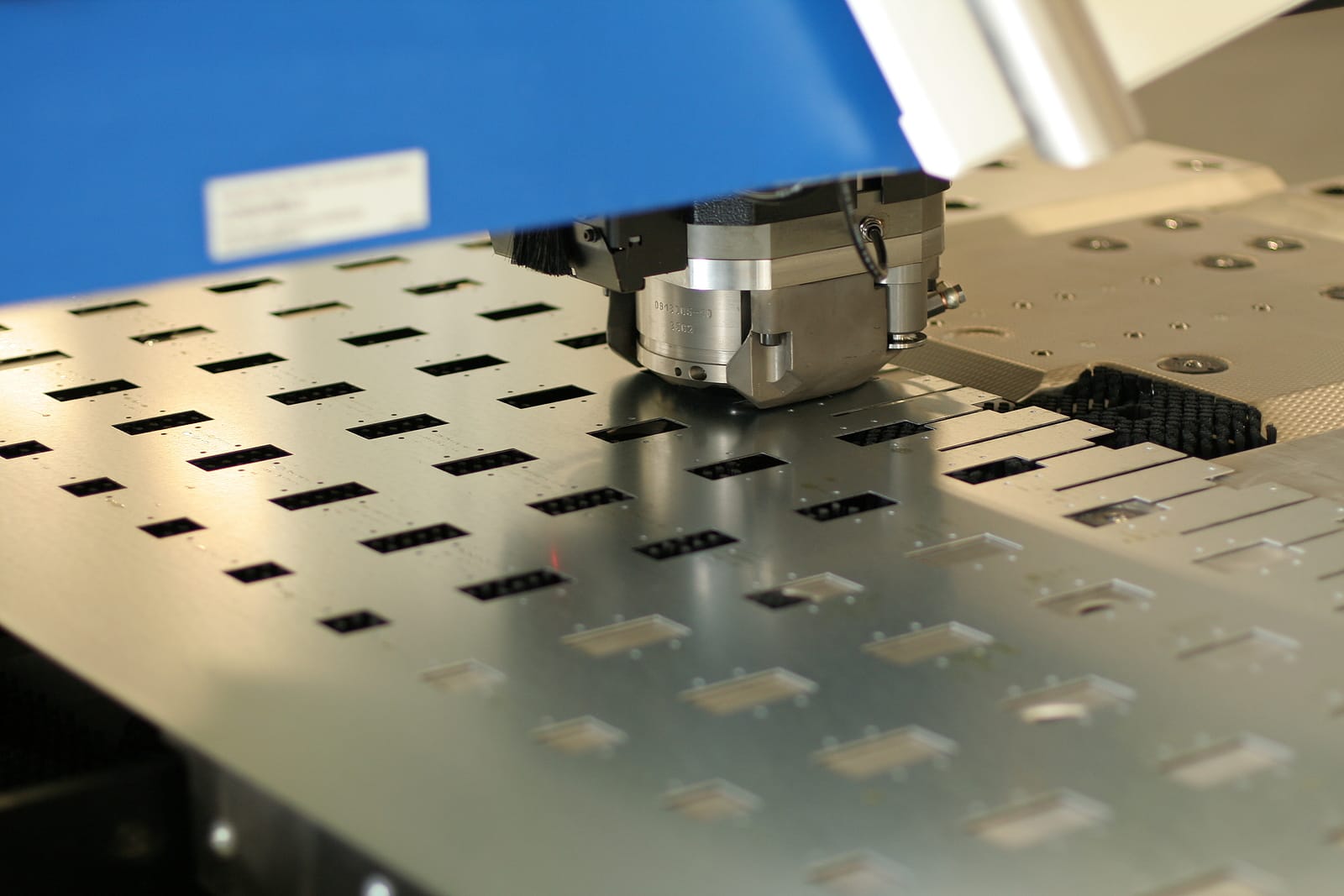
Introduction: What is digital transformation, and how does it affect the metal industry?
The transformation of the metal industry has been in process for some time now. With the emergence of new technologies, the industry is changing faster than ever.
It's the process of transforming the way an organization does business, providing a better customer experience with digital technology, and involving all facets of an organization (such as IT, marketing, customer service, finance).
It is about using digital technologies to innovate on what you do best. It can help organizations transform their business models and improve their competitiveness. Digital transformation is not just an IT thing; the metalworking industry has to transform in order to stay relevant.
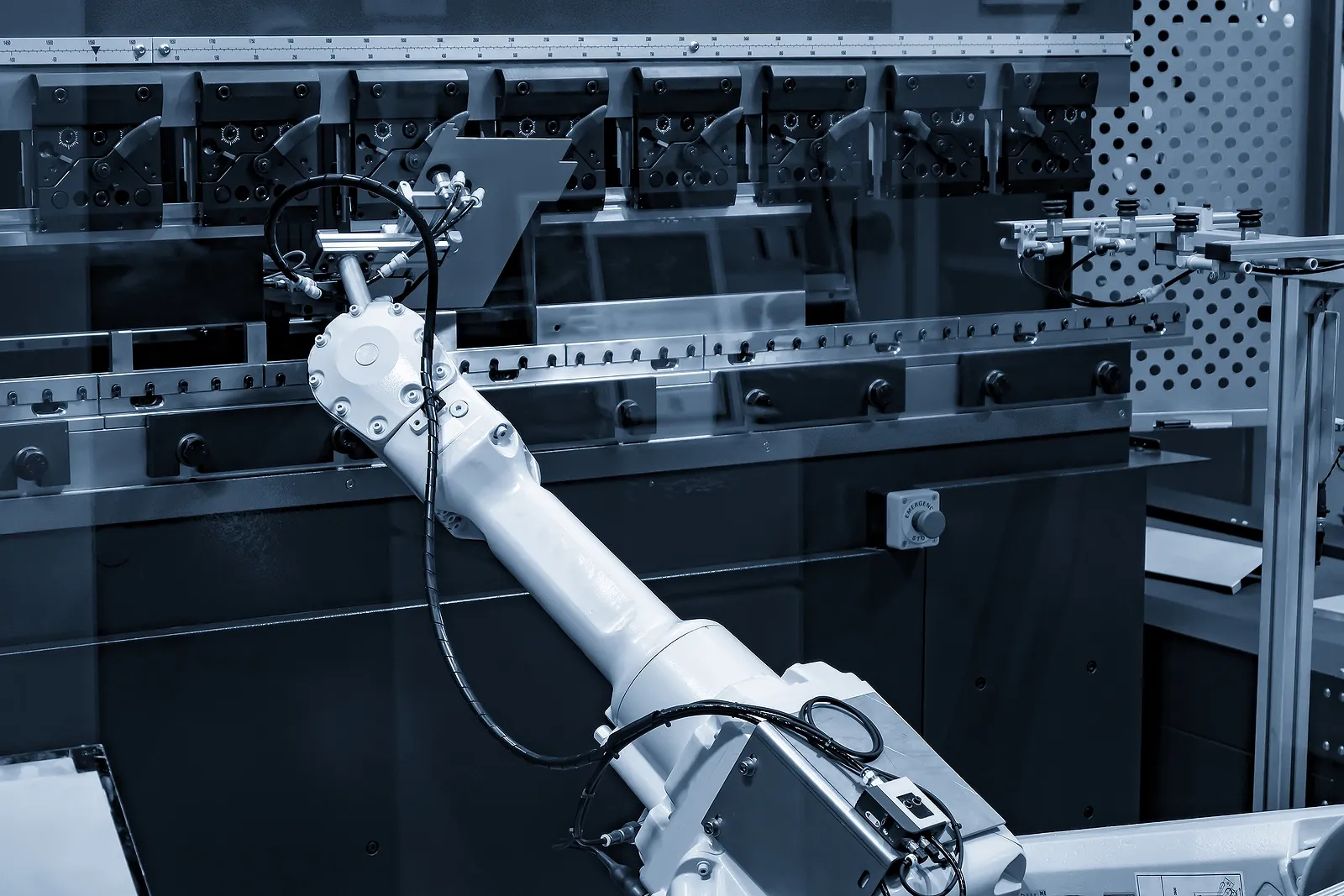
Mistake #1: Misunderstand Industry 4.
Industry 4.0 is not just about replacing people with robots. Industry 4.0, also known as the fourth industrial revolution, is a rapid transformation in the way we work. The market for Industry 4.0 technologies is vast and expanding rapidly. This revolution is gaining increasing popularity across industries.
What is the fourth industrial revolution?
The industrial revolutions are briefly described as:
1. Industrial Revolution: Hydropower and steam engines
2. Industrial Revolution: Electricity and assembly line manufacturing
3. Industrial Revolution: Automation through computer technologies
4. Industrial Revolution: Digitalization of analog techniques and integration of cyber-physical systems
As you can see, all previous revolutions revolved around physical inventions such as machines and technology.
This time, however, the real innovations are in the field of digitization and connectivity.
It's less about physical inventions and more about reinventing the way software and sensors work together. It's about how the latest developments in Artificial Intelligence, Big Data, the Internet, and Smart Devices are all interacting together.
Industry 4.0 is the latest industrial revolution. Computers work directly with automation systems, eliminating the need for agents, middlemen, and additional staff. The change aims to automate manual tasks and achieve reliable results.
At its core, it's about a new approach to using software to reinvent our business.
What can go wrong if you misunderstand it?
Most manufacturing companies are unaware of what Industry 4.0 means in practice, its origins, and how to achieve it. Consequently, they continue to work with outdated systems and invest in them.
There's a significant risk that, without realizing it, you're still purchasing Industry 3.0 solutions. Perhaps you're considering buying new software, and unknowingly, you're burdening yourself with a legacy product that's already outdated by the time you go live.
Even worse, you might completely neglect the trends and keep focusing solely on hardware, machines, and tools, instead of the software aspect of your business.
Most successful companies will rely on the quality of their software, not the physical machines they own, unless they operate in a low-wage country. While it's easier to stick to the familiar, it seems more rational to explore the risks of the unknown. Unfortunately, some vendors take advantage of this by selling "Industry 4.0 solutions" when it's the same technology as it was 20 years ago.
It is common for budgets for machines to be high, and since they are physically tangible products, this budgetary decision can often be more easily justified to the CFO.
However, when a software package – a materially intangible good – costs almost as much as a machine, companies often fail to see its value. This is an example of falling into the pitfall because if the CFO were educated in Industry 4.0, the decision should be weighed equally to a software investment.
What to do about it?
Remember: We are primary in a software revolution.
Avoid thinking exclusively in terms of machines instead of software these days. Also, don't try to look for software solutions with decades of history, as they're probably outdated.
In retrospect, you wouldn't take someone who invested in oil lamps instead of electricity during the Second Industrial Revolution as a role model. They forget—or are often simply unaware—that today's age is about software that makes the difference.
The most important thing for metal companies is to serve their customers effectively by reducing manual activities as much as possible. The only way to achieve this is to utilize the right software tools that can be reliably integrated.
The best way forward is to get educated about the optimal software solutions and strategies within the industry.
Here at Sheet Metal Connect, we provide a wide variety of independent reviews and articles, such as the best ERP for metalworking and best CAD-software for metalworking.
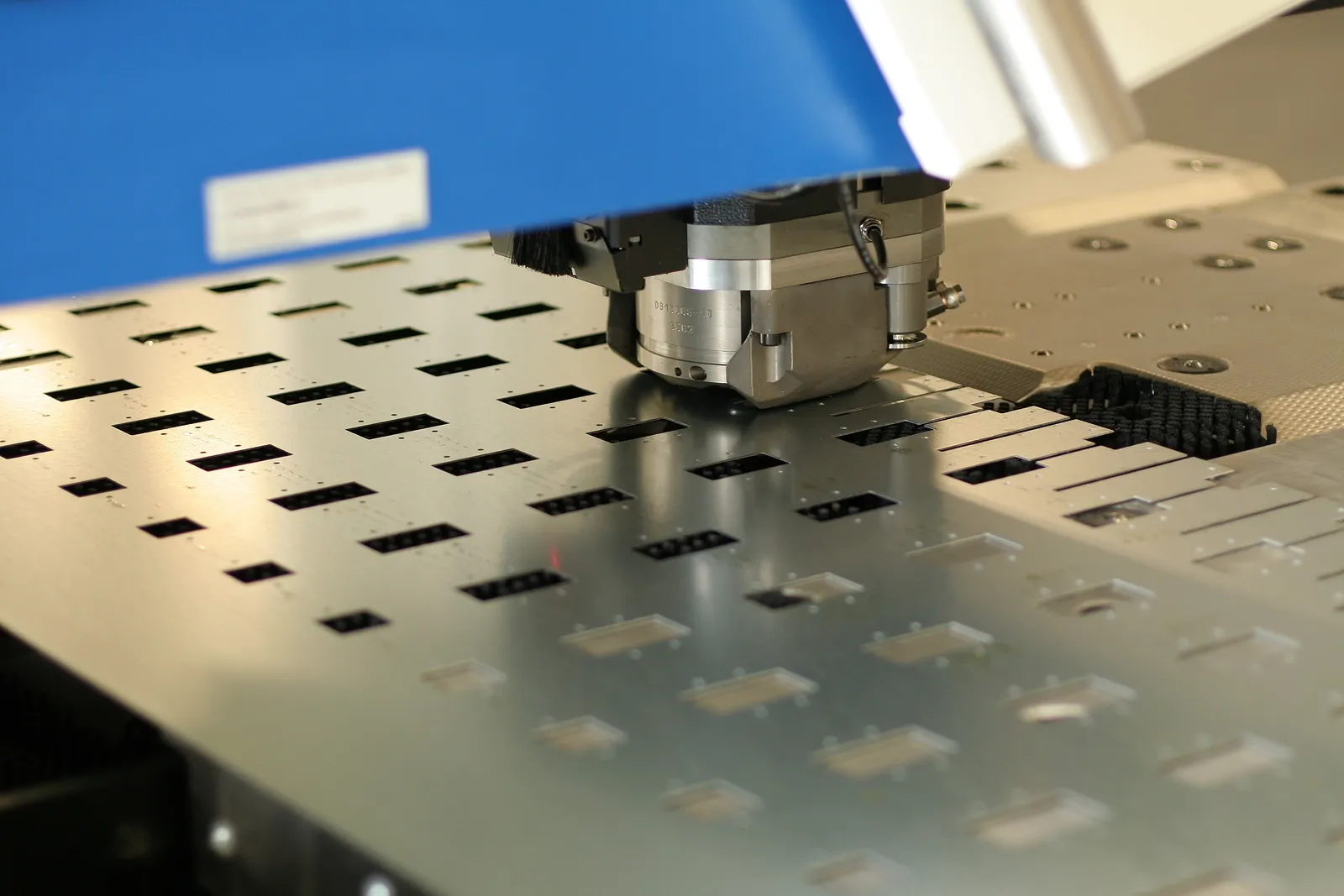
Mistake #2: Failure to align your business model with your customer model
"If I had asked people what they wanted, they would have said faster horses." - Henry Ford (assumed author)
Some people say that it was Henry Ford himself who first mentioned the famous "faster horse syndrome," while others think it was one of his collaborators. Unfortunately, they cannot agree on who said it, as the person deserves recognition for having such a brilliant thought.
The idea is that people often think in terms of what they know. If you're holding a hammer, you're probably looking for nails to hammer. Sometimes you don't need a hammer or a screwdriver, but a key that will open locks.
What we mean by this is that it's common to automate a factory, but then forget to look for new customers for the new automated plant.
The risk for most companies is that when faced with change, they constantly look for the things they know, rather than what they truly require or, even better, what they can do with that new change.
The vast majority of entrepreneurs in the metal industry are still in the third industrial revolution: automated production lines that produce the same products as efficiently as possible.
It's no longer about the high variety or dynamic scheduling required these days. It's often a matter of reacting to situations rather than anticipating them.
What can go wrong with an outdated business model?
In Industry 3.0, the processes and systems were designed for large batch sizes with only a few customers who did not change products frequently or have a continuous order flow. Inventory was the industry standard, and the larger the order size, the better.
The more you could make at once, the better.
However, now there is the customer of the 21st century. That other customer is no longer there because they either moved to a low-wage country or simply no longer need large continuous flows.
Even the automotive industry is now changing designs at record-breaking speeds.
You have probably already noticed the change that has taken place in your company: batch sizes are shrinking rapidly, customers want their orders just-in-time, designs are changing more frequently, and planning all these requirements is becoming increasingly complex.
Not only is the logistical design of your factory likely not designed for this new type of demand, but your software solutions are probably not either.
It is therefore also important to admit that although they are large, it no longer makes sense to concentrate only on a few customers. If you focus solely on better serving these few large customers, you're missing out on an indispensable development in your industry.
How to avoid the business model mistake?
Think about how you can better serve your new customers with today's market services: faster deliveries, faster responses, and digitally connected services. You must consider everything that makes your company unique, including the machines, employees, orders, and software.
For metalworking businesses that serve customers with custom products, Industry 4.0 is about quickly developing new solutions for your customers and ensuring overall productivity is improved.
My customers have achieved this and realized that producing products with low volume and high variety and complexity is actually more future-proof.
Don't just focus on process improvement philosophies like LEAN (to avoid waste), but broaden your perspective and investigate options for becoming more efficient than the competition, such as Quick Response Manufacturing (QRM). Consider working more intimately with your customers and vendors by connecting to digital supply chains and exchanging real-time data.
Lastly, exploring a servitization strategy means increasing the offer of product and service packages focused on customers and their businesses. Turn your factory into a Factory-as-a-Service. In simple terms, servitization refers to industries using their products to sell "outcome as a service" rather than a one-off sale.
Mistake # 3: Getting stuck with sunk costs
Do you still have your CDs of Windows 95 somewhere? Or perhaps the first DVD player you ever acquired? Chances are if you did, you understand why it's hard to let go of things that you don't (really) need anymore, right? Why do we keep holding on to things that don't serve us anymore?
It's a problem that happens on a massive scale in the industry. Keeping old machines, continuing to update already written software systems, and clinging to Excel sheets, while they are already easily available in modern solutions such as ERP, CAM, and MES.
Of course, it makes sense: If we spend a lot of money on (for example) a software system, it becomes much harder to let it go, even if it no longer makes sense to continue with it.
It's not always easy to predict what Industry 4.0 solutions will bring, and software is not as easy to understand as mechanical processes. What is often overlooked is that the price a company pays for this approach is getting ahead, and this is a far more expensive cost! The reason for this lies in the misconception about "sunk costs."
How sunk costs block progress
Let's look at an example of this in practice. A factory wants to start with new systems and digitization. A team is quickly formed, and the providers are selected. However, as soon as the budget is discussed, resistance arises.
- "But what do we do with the current system?"
- "This self-created software that took so many working days? It certainly cost a fortune! Can't we further optimize what we have?"
- "Was it all in vain?"
- "We've already invested so much, now we can't stop."
So, what do you do?
Chances are there is always someone who will mention how risky the future is and why the current thing still works fine. And there it goes! Your great plans fall into nothing, and we go back to the old ways.
How to get over sunk costs
The reason for skepticism about new things is easily explained: a loss makes us twice as unhappy as a comparable gain makes us happy. From an economic perspective, the decision is straightforward.
It's all about the difference between what you have now and what you'll have in the future. Whether it makes sense to proceed with anything depends on all future income and expenses. If this leads to a positive overall balance, it makes economic sense. Otherwise, it doesn't.
Therefore, whenever you encounter this discussion, pause for a moment and ask yourself:
- “What will we miss out on if we don’t change?”
- “What can we achieve if we DO let go of the past?”
- "Are we overrating this project because of our emotions?"
- "What is the best decision for our customers for now and in the future?"
- "How much value will this still have in 5 years?"
Often the best conclusion is that the current setup has served its purpose for the time being, but times have changed, and now the actual value is probably much lower than the emotional value that was given to it.
What helps is an independent analysis of the big picture and a plan for the future based on data, without emotional attachment to the old system, but solely based on facts and research results.
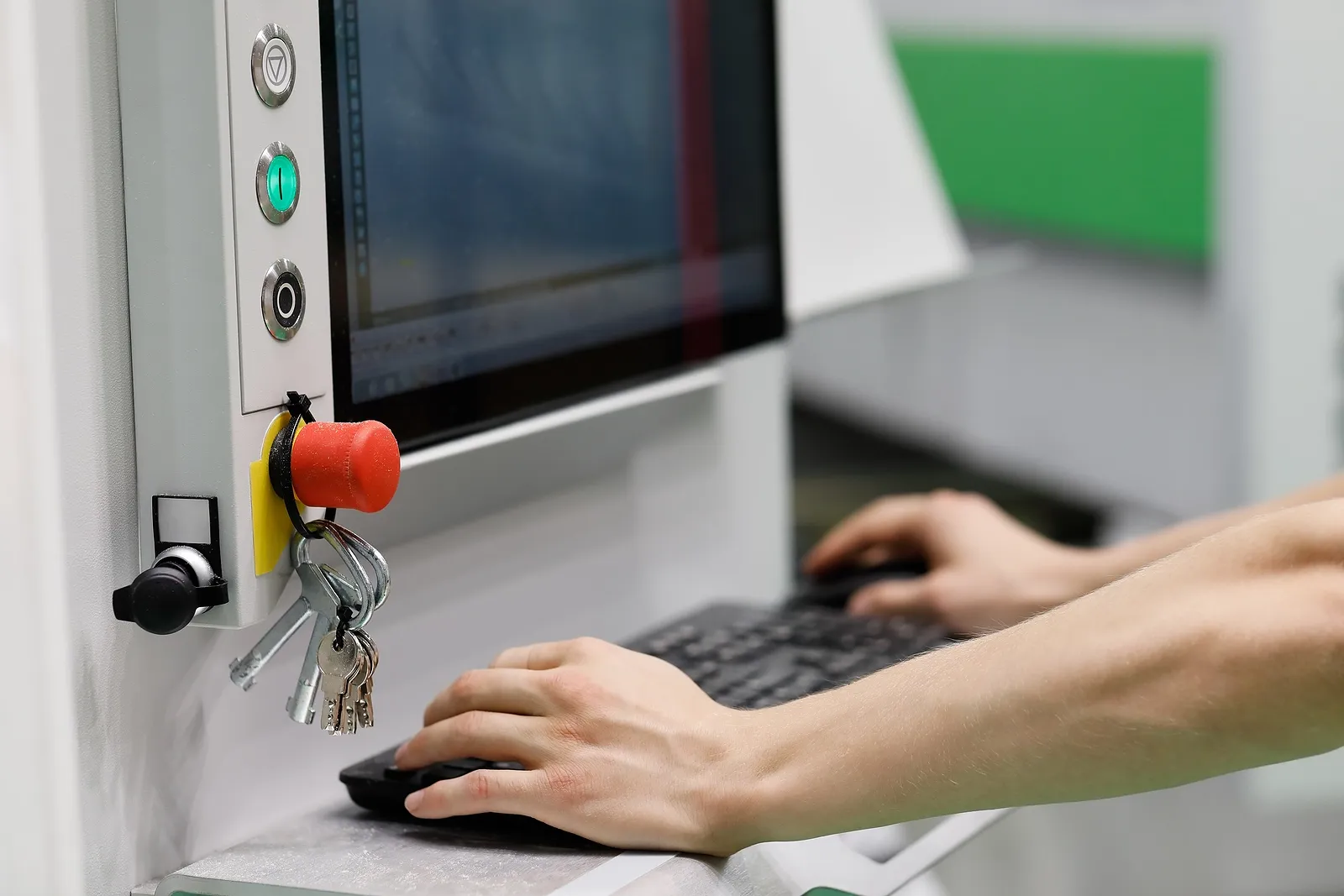
Mistake # 4: Failure to keep data organized
A significant aspect of Industry 4.0 is the digital transformation: the transition from paper processes to digital processes. However, it's not merely about eliminating paper but also about defining new ways of working.
As you can see, the terms digitization and digitalization together result in digital transformation.
Digital transformation is usually gradual, with certain parts of the business being changed step-by-step. Rarely do companies have the financial means and focus to completely transform in a short period.
A step-by-step transformation offers many advantages. One important point is that there is time to learn from the process. Additionally, employees can gradually adapt to the new working methods and systems.
However, a gradual transformation has a catch: many do not know which parts to digitize, and so you may exchange one evil for another.
Essentially, instead of a stack of paper, you have a new "data stack" somewhere.
The result: you no longer know what information is stored where and what happens when you want to replace a system. This creates a kind of "IT-hell" where there is no longer an overview.
The "IT-hell" of a data jungle
Does the following sound familiar?
- Is your office team handling 3-5 different software programs to understand what a project entails and what needs to be done? Is this sometimes even combined with paper storage?
- Does one database or file indicate that the design is the latest, while another says that the customer submitted a revision months ago?
- Have you inadvertently produced products incorrectly, made orders with incorrect quantities/materials, shipped multiple times, or even unintentionally placed duplicate orders?
If any of these things sound familiar to you, you probably already have a data problem!
The more software is implemented, the more data is generated, and for this to work for your business, it all needs to be integrated.
What is often forgotten when implementing new solutions is that they must work with the entire company, including the supply chain.
When this is neglected, it becomes a chaotic situation where no one really knows how things work together.
How to Keep Data Organized
To counter this increasing confusion, you need to centralize all your data. As a rule, this is done by linking all systems to the ERP (Enterprise Resource Planning) software, ensuring that only one system is the leader.
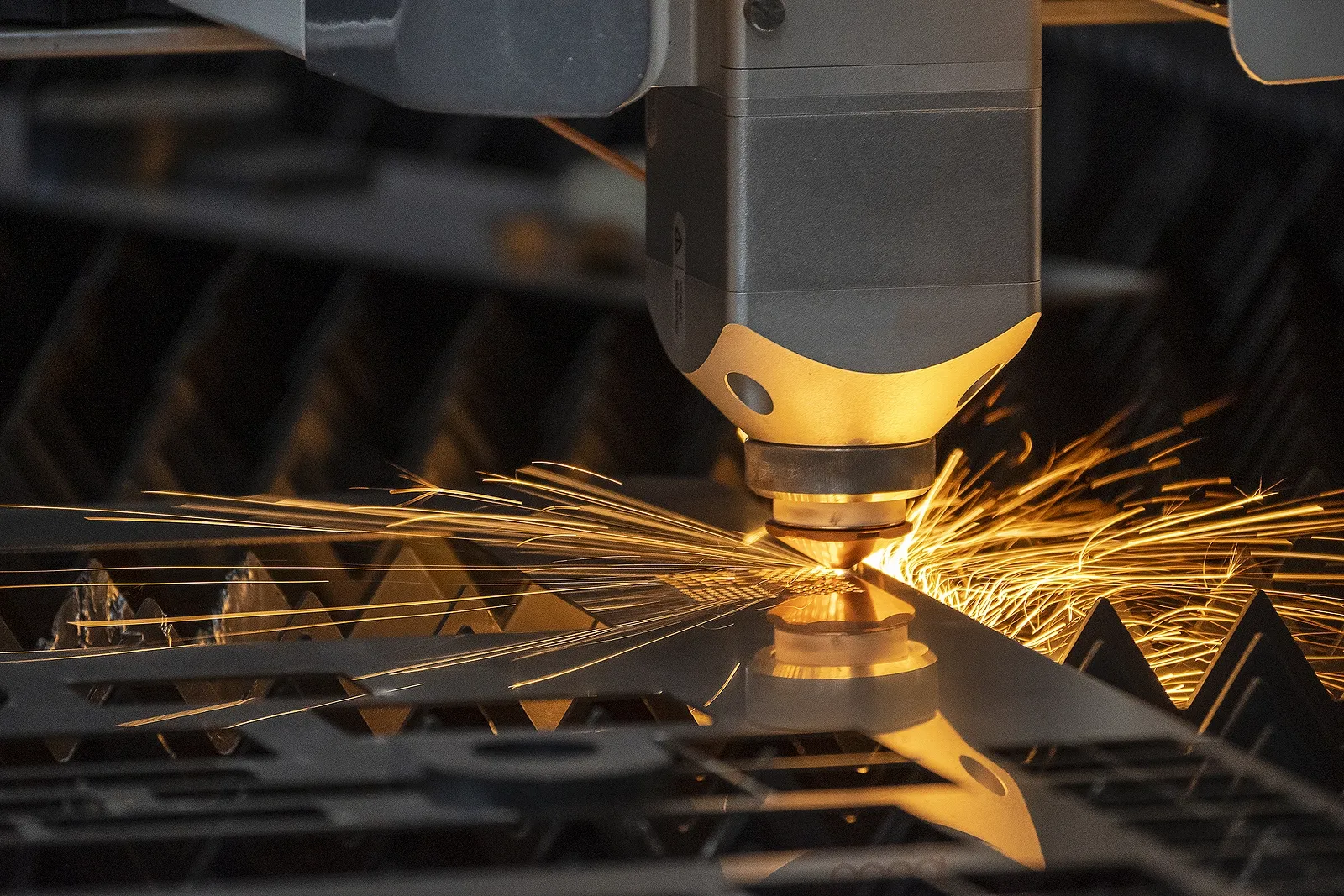
Mistake #5: Failure to plan for cybersecurity risks
When you introduce new software, tools, and even consultants, you bring security risks along. Outdated Windows systems (the software on your machines) pose a high risk.
Most companies can start by installing software, but one of the most common cybersecurity mistakes is not planning for cyber risks.
The biggest mistake in data protection is not taking steps to prevent data breaches. The best way to avoid this risk is by implementing strong security measures when designing or upgrading any systems.
Another common mistake when it comes to GDPR compliance is failing to follow the rules in the legislation regarding customer consent. Failing to comply with GDPR can lead to heavy fines, which can prove costly for businesses of all sizes.
Conclusion: Start Making the Shift Towards a More Innovative Future Today
In this article, I have discussed some of the most important aspects of digital transformation, including its necessity and how you can achieve business success.
Now that you know the 5 pitfalls to avoid in digital transformation for metalworking, you're ready to move your factory to the next level without worrying about doing it correctly. Digital transformation is undeniable.
There are many benefits of digital transformation, and it is something we need to embrace and implement as soon as possible if we want to succeed in the future. If you'd like to learn more about our services, please see the links below.