Introduction: The basics of digital factory software
Why do you require software for your business? In short: So the system can work for you, without you having to spend more time on it.
The idea behind a digital factory is that everything is connected and that you, as the business, can reduce manual actions while increasing outputs.
More advanced development will help you also have software predict things, execute automatic actions, or even create self-learning systems.
So, the basic concept is that you have on the one side modern software systems that work effectively and on the other side a connected system that allows data to flow from one system into the next.
Finding the right solution for you
If you're looking for software for your manufacturing business, the best way to ensure you're getting something that helps you increase your productivity is by looking for these things in your factory:
- Make sure your factory is built upon modern software solutions that can be easily integrated over XML or APIs. If not, you'll have to retype countless data and won't achieve efficiency goals.
- Ensure your factory has a clear process description on how you will work with the software so that you are achieving consistent output.
- Any good software vendor will allow you to test and try out their solutions. This is important because you need to make sure you'll enjoy using the solutions.
Table of contents
- 3 Important benefits of digital factory software for metalworking industry
- 7 Software types every metalworking business needs
- #1: Computer-Aided Design (CAD)
- #2: Computer Aided Machining (CAM)
- #3: Enterprise resource planning (ERP)
- #4: Shopfloor Control (SFC)
- #5: Manufacturing execution system (MES)
- #6: Product data management (PDM)
- #7: Business intelligence (BI)
- Action steps
3 Important benefits of digital factory software for metalworking industry
Digital factory software has many benefits for the metalworking industry.
The first benefit is that it can help companies improve their product quality and consistency. This is significant because customers often reject products that do not meet their standards or expectations.
The second benefit of digital factory software is that it helps companies reduce waste and increase efficiency by automating many tasks, such as cutting and welding. This means there will be less human error, which will result in higher quality products with less waste materials.
Digital manufacturing also saves time because companies can produce parts much faster than before due to the automation of tasks such
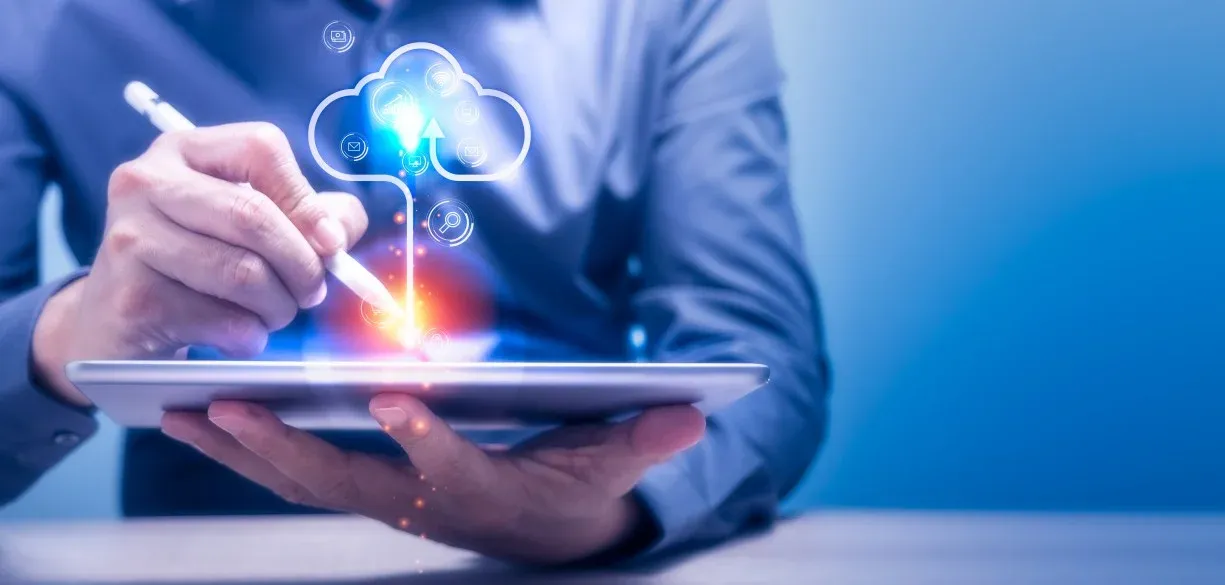
7 Software types every metalworking business needs
In this chapter, we've outlined 7 types of software you need in your metalworking manufacturing business. They are sorted in chronological order, from your start-up job shop to larger manufacturing plants with custom products and often multi-factory challenges.
Of course, every company is different and if you are unsure of what works for you, reach out to us for a free advisory conversation.
Now let’s dive into the software types.
#1: Computer-Aided Design (CAD)
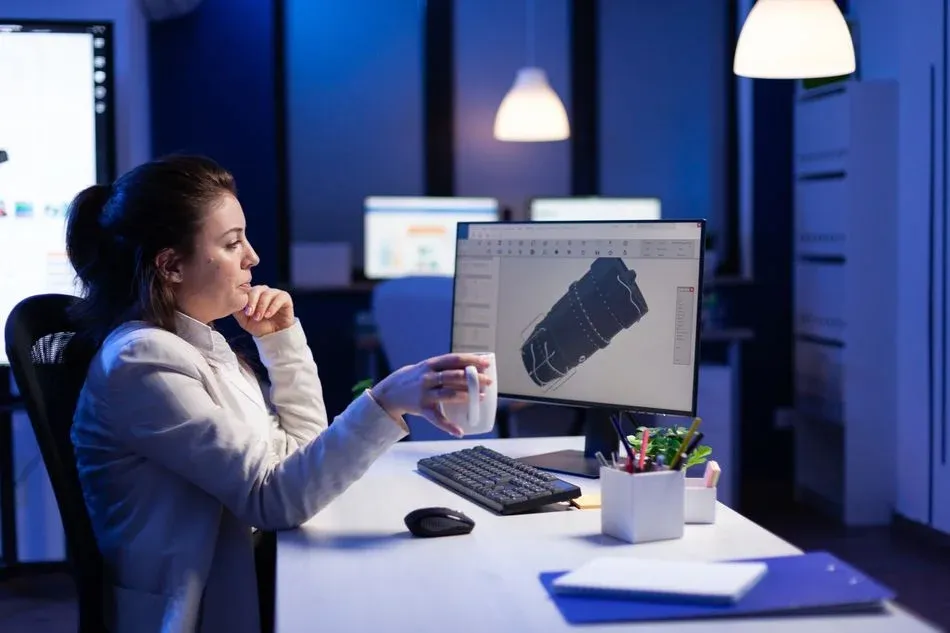
CAD software is 3D modeling software used by engineers, architects, and various other types of professionals to create prototypes. It can be used for 2D or 3D modeling, manufacturing drawings, technical drawings etc.
Commonly used brands in the industry are AutoCAD, Inventor, Fusion360, SolidWorks, OnShape, and SpaceClaim.
The first thing you'll work with as a metalworking company is drawings, whether they're handed to you in PDF or CAD files. It's very common that you'll have to start making your own designs or adjust customer designs very early in your business. That's why CAD software is usually the first investment any metalworking company will make.
If you’re just starting out, then lucky for you, we’ve outlined free CAD-software in another article.
Basic CAD systems are often used stand-alone, meaning they are used to draw and print work instructions. For this type of system, a smaller budget is typically sufficient.
But modern CAD-software systems, such as SolidWorks, Fusion360, and Inventor are typically integrated with CAM (or even ERP) systems. This all makes the workflow more efficient but also increased the price tag. It's important to consider the current size and goal of your company when deciding what package to start with.
#2: Computer Aided Machining (CAM)
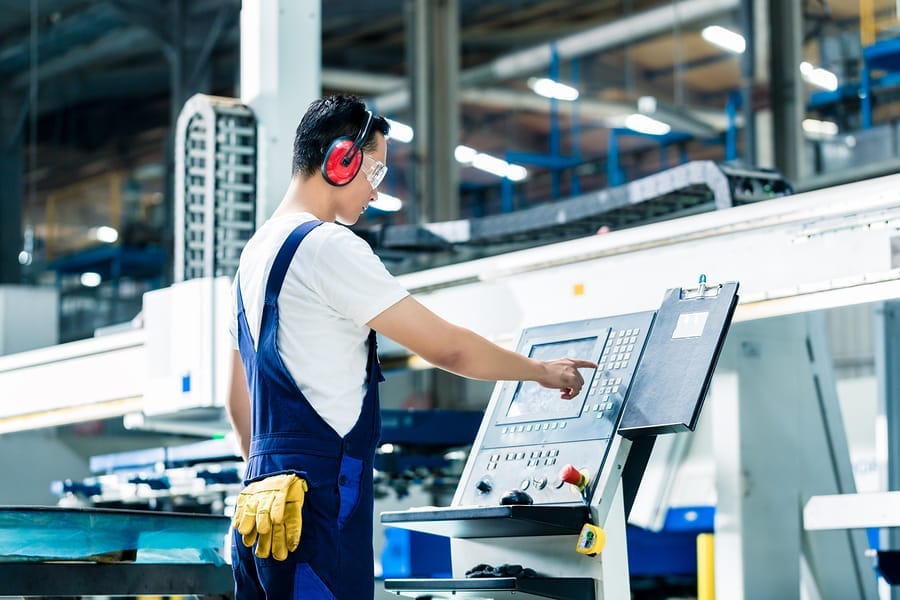
The second software you’re probably getting started with will be Computer Aided Machining (CAM). It’s the use of software and computer-controlled machinery to automate a manufacturing process. It simulates production and creates the tool paths for your machine.
Because it can automatically generate the tool paths, which means that CAM users don't have to manually create them. This saves a lot of time and energy, while also increasing productivity.
CAM is a very significant aspect of the manufacturing process. The software will not only create tool paths, but also simulate production in advance, to help reduce discrepancies in the final product by calculating things such as feed rate and the appropriate tool for a particular project.
In (sheet) metalworking, CAM-software is necessary to operate most CNC-machines and often are coming with the machines you’re buying. However, if you have multiple machine brands, you need to look into either universal systems or post processors.
#3: Enterprise resource planning (ERP)
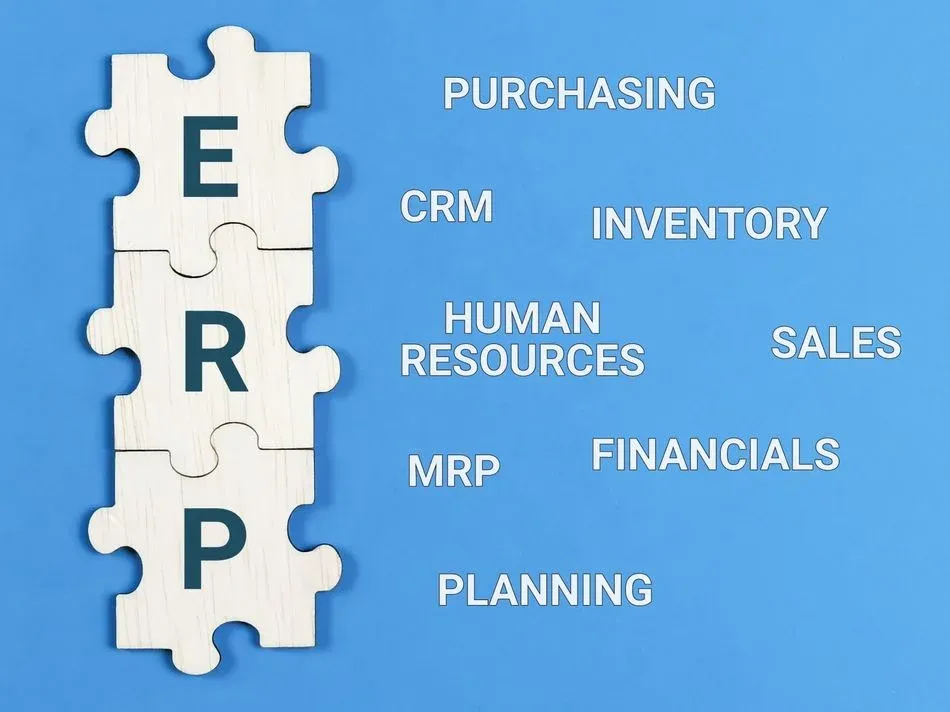
Enterprise resource planning (ERP) is what most businesses use to manage day-to-day business activities such as accounting, procurement, project management, risk management and compliance, and supply chain operations.
This is probably a system you’ve heard a lot about. ERP comes to mind for most factories when they feel like they can no longer remember things, are losing the overview, and it starts to slip through the cracks.
For most companies, this is where most of their focus (and often their frustration) lies. It's no surprise, since the ERP market is a billion-dollar industry with a lot at stake for both vendors and manufacturers.
ERP is a must-have asset for any serious metalworking business, and typically, when you're as small as 5 employees, it's time to get on the bandwagon now. You probably won't stick with one system forever, so our advice is to avoid customization as much as possible and aim for integrated solutions.
If you're wondering what to use for your business, check out our guide in the link. We've written an extensive software guide for the BEST ERP in the market.
#4: Shopfloor Control (SFC)
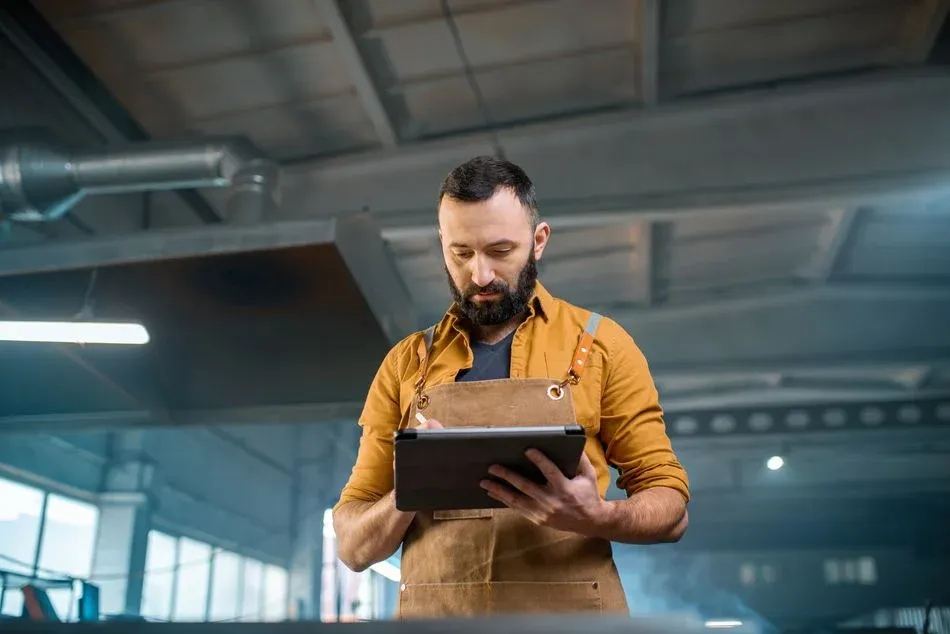
If your ERP is up and running, it doesn’t make sense anymore to keep printing work instructions all the time. Working with paper clocked hour lists and such.
Your staff can find their work by logging into tablets and computers on the shop floor. That’s where your shop floor control steps in: computer devices on your shop floor that the operators can manage their day-to-day business, without the need for paper and constant supervision.
Shop floor Control (SFC) is a system of tools used to schedule, dispatch, and track the progress of work orders through manufacturing based on defined routings. It is commonly combined with quality reporting and stock level inventories.
The SFC system is designed to provide management with an overview of production, while enabling operators to work more efficiently. It also helps them to identify problems in the production process.
For sheet metalworking companies, you'll have to consider how much of your work will be managed by shop floor vs what machines and their interfaces can take care of.
For example, if your laser-cutting machine already has an interface that tracks the hours worked per nesting, it's often smarter to move some of those tasks into your MES system (see below).
#5: Manufacturing execution system (MES)
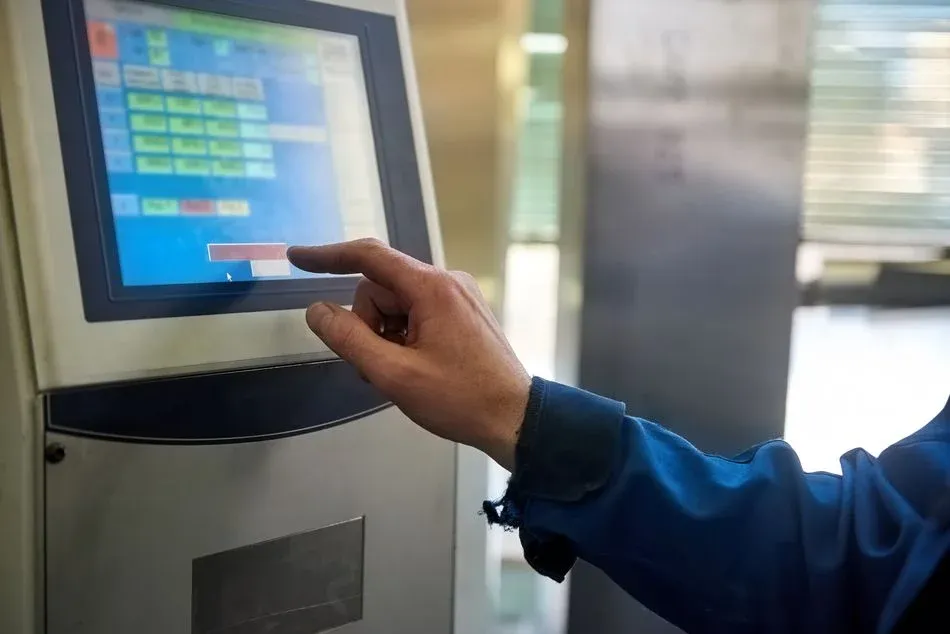
Once your factory is running and multiple machines, robots or even production locations start to come in the mix, it becomes quite challenging to manage the business with paper. Matter of fact, ERP will also reach its limits pretty soon when it comes to quality management, scheduling, and job controls.
Manufacturing execution system (MES) is a software system used in production that controls and records the transformation of raw materials into finished products. A MES provides information that helps make decisions on how to optimize production based on the current conditions of a production plant.
Manufacturing Execution Systems (MES) provides the essential capabilities and features that will allow manufacturers to control all aspects of production, from scheduling and routing to quality control and more.
#6: Product data management (PDM)
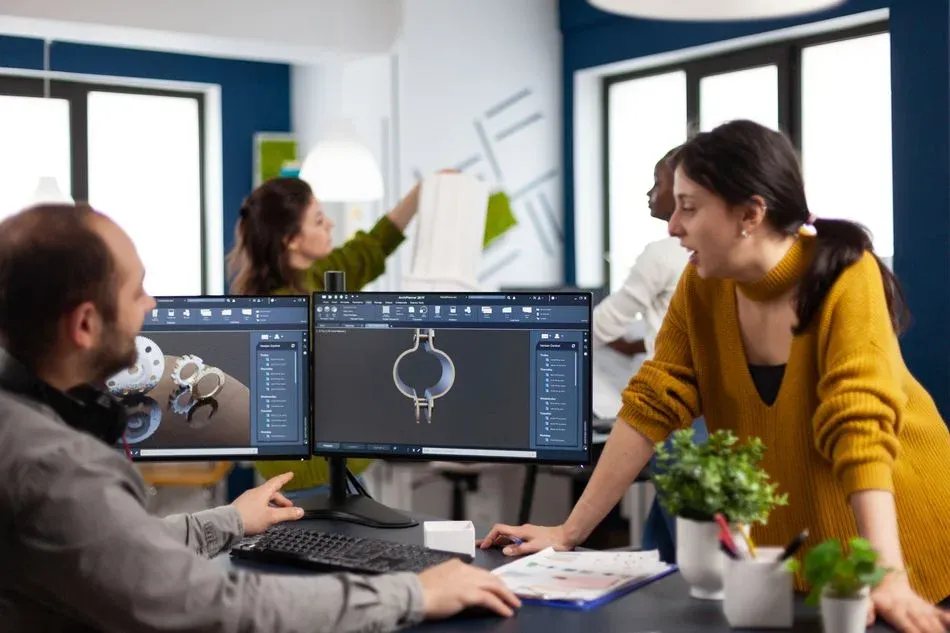
Product data management (PDM) is a system for managing design data and engineering processes in one central location. It’s used by Engineering teams to organize product-related information, track revisions, collaborate, manage change orders, generate Bills of Materials (BOMs), and more.
In short: it allows you to keep a good overview of your designs, without getting stuck with your default Windows Explorer, and all its problems.
For sheet metalworking companies, this will be most often used to store complex assemblies and their revisions. If your factory designs its own products, it is vital to manage changes in designs and keep an accurate history of this.
PDM systems are typically connected to CAD systems, which in turn are connected to ERP systems. With PDM systems, you can typically also create batches of files, such as plotting PDFs and DXFs for production. Software you should check out for this are OnShape (as part of their CAD-suite) and Autodesk Vault.
#7: Business intelligence (BI)
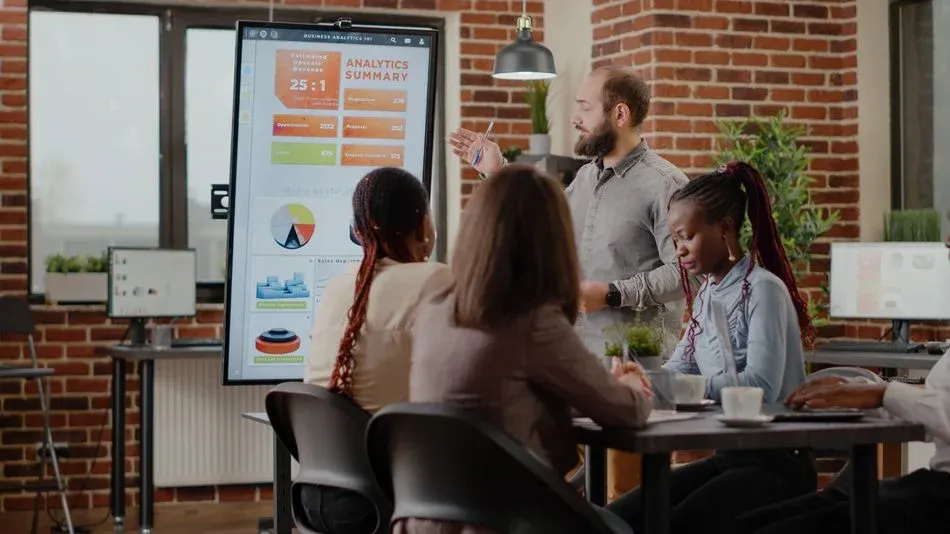
Business intelligence (BI) is a powerful technology that can be used for either internal or external purposes. BI gives you the power to turn your company's data into information that provides actionable insights and guides strategic decision-making.
BI is often overcomplicated in its explanation, and what it comes down to is that you can create charts and tables that are combining information from many sources. Examples of what you can do with this solution are: OEE dashboards, quality monitoring, revenue trends, stock levels and predictions, and delivery performance.
You can do this by combining data from many tables in your ERP system without having to code. Or, even better: combine data from ERP, CAM, MES, and more.
You might think, "Why can’t I do this with Excel?" And yes, you can do this on a limited scale with Excel, but if you want to have more flexibility and save time, you're better off with BI software.
The most important reason is that BI systems can detect relationships without any coding. For complicated queries, simplified scripting languages have been developed, such as DAX for Power BI.
Our favorite software for this is Microsoft Power BI, which even comes in a free tier. For the paid solution, you don't have to break the bank, either. Other software that you should consider are Qlick and Tableau.
Action steps
Now that you have an idea about what kind of software you need for your business, you're ready to start building your ideal factory without getting confused about the different vocabulary in the industry.
Let's, in conclusion, close this article with a few questions about your business. Take a bit of time and consider the following:
- What current software are you using?
- What kind of software is it?
- What software functions are overlapping? Are some systems taking on multiple roles?
- How satisfied are you with the current software systems?
- Where does the system underperform?
- What’s your biggest obstacle to increasing your output?
- What software do you miss from this list?
Now that you know the basics, you can investigate what steps are necessary to improve automation. It can help a lot to get advice for your strategy. Lucky for you, we offer a free introductory consultation to sheet metalworking companies.