Have you ever gone on the search for a new ERP-software system for your metal fabrication business?
If so, you know that it is difficult because there are many vendors out there all claiming they have the perfect solution, but you also hear about the horror stories of failed implementations.
So, what do you do?
Many people have been able to find success by starting out with an early independent analysis of ERP software systems, such as this guide.
Before you buy and implement an ERP system, there are a few things you should know to make sure the project doesn't result in frustration, or worse- a failed project.
To help you get started, we’ve crafted this 100% independent and personally curated comparison of the top 10 ERP systems for metal fabrication.
We are convinced that will help you select which one will help you increase the efficiency of your business on the short term and for the years to come.
Here's the list (in alphabetical order):
Software | Provider | Product Information |
---|---|---|
Bemet | ECI Software Europe | Bemet |
Business Central | Microsoft | Business Central |
BySoft Business | Kurago Software | BySoft Business |
Fulcrum Cloud | Fulcrum | Fulcrum Cloud |
Genius ERP | Genius ERP | Genius ERP |
Infor M3 | Infor | Infor M3 |
JobBOSS² | ECI Software Solutions | JobBOSS² |
Odoo | Odoo | Odoo |
Priority ERP | Priority Software | Priority ERP |
Ridder iQ | ECI Software Europe | Ridder iQ |
Modern ERP for Fabricated Metals
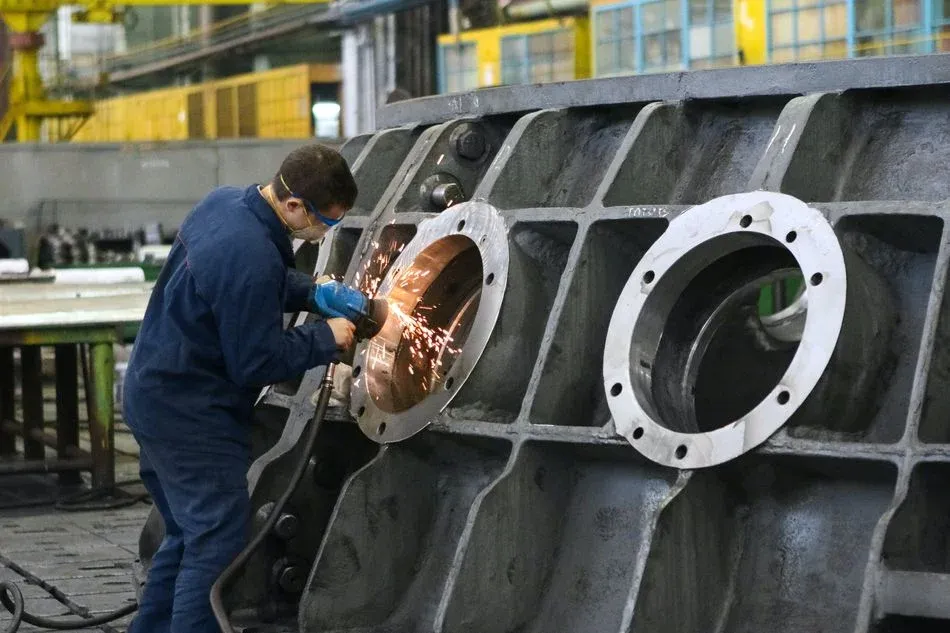
As global supply chains become more complex, the fabricated metal industry must find efficiencies in new technologies and processes.
Traditional practices have proven to be inefficient with the increasing level of complexity within these global supply chains.
Already thin margins are being further threatened by rises in raw material costs, shorter product lifecycles, and more stringent quality standards.
Many organizations are looking to adopt lean initiatives to bring down costs, reduce waste, and realize efficiencies across their complex supply chain to remain profitable. This might not be enough, though, and that's where modern ERP for fabricated metals manufacturers comes in.
ERP is an integrated, powerful suite of software for an organization's operations. It helps the organization to manage its workflow and help automate many processes.
What are the benefits of metal fabrication ERP software?
An ERP software for metal fabrication can provide many benefits. It can help with production and inventory management, which in turn will lead to a better utilization of resources and a more profitable business.
A metal fabricator who installs modern ERP software correctly can increase production output and without having to hire more staff. This will make it easier for the business to grow and be more efficient with operating costs.
It provides better inventory management and control, which makes it easier to forecast finished products. It also streamlines production planning and gives businesses more overview and control of their operations.
Do you want to read more on ERP systems in general? You might also want to check out our other article: Why Enterprise Resource Planning (ERP) is important for metal fabrication
What are the must-have software components for metal fabrication?
Metal fabrication is a form of discrete manufacturing. It’s a manufacturing practice that operates with bill of materials (BOM) to make individual parts of a product. The pieces are then often merged to form the final product at the end of production.
Therefore, metal product manufacturers face some unique challenges in their production units due to BoM's and routes that are typically only partially defined, and a strong engineering function that governs product design.
There is usually a low-volume, high-mix approach, which requires data entry to be swift and ideally automated. For high-volume manufacturing, for example for cost-competitive laser centers, it is typically a challenge to deal with correct inventory levels, both in materials and finished products.
Planning to achieve shorter lead-time items and ensuring work is scheduled through the production facility in a timely and efficient way are key to success in this sector.
The right ERP software can help you save time and energy, as well as drive your success as a company. But why should you choose an ERP software over other alternatives? To answer this question, we must first know what the requirements are for a good choice.
Below, we’ve listed modules that we consider as must-haves and recommended:
Must-have modules for metalworking:
- Bill of Materials (BOM) and routing, often with support for Assembly structures.
- Material Requirements Planning (MRP)
- Customer Relationship Management (CRM)
- Sales and Purchase order processing
- Basic inventory management (raw materials)
Tip: Make sure your BoM allows you to create relationships between materials and operations. If it doesn't, you will have trouble creating integrations with your CAM-software.
Optional but recommended modules
- Product configurator and Product Data Management (PDM)
- Purchase requisition
- Pricing and quoting
- Shop floor control
- Time and attendance
- Financial management
- Enhanced Inventory Management (both finished parts and materials)
- Part tracking and traceability
- Quality Assurance / Quality Control
- Production Management
There are, of course, many more modules. For example, vendors often combine their ERP-offering with Manufacturing Execution Systems (MES).
This can be tricky, since there can be quite some overlap in functionality between ERP and MES. In general, it might be wiser to look for these features later down the line. When in doubt, contact us, and we can discuss your particular situation.
How to select the right software for you
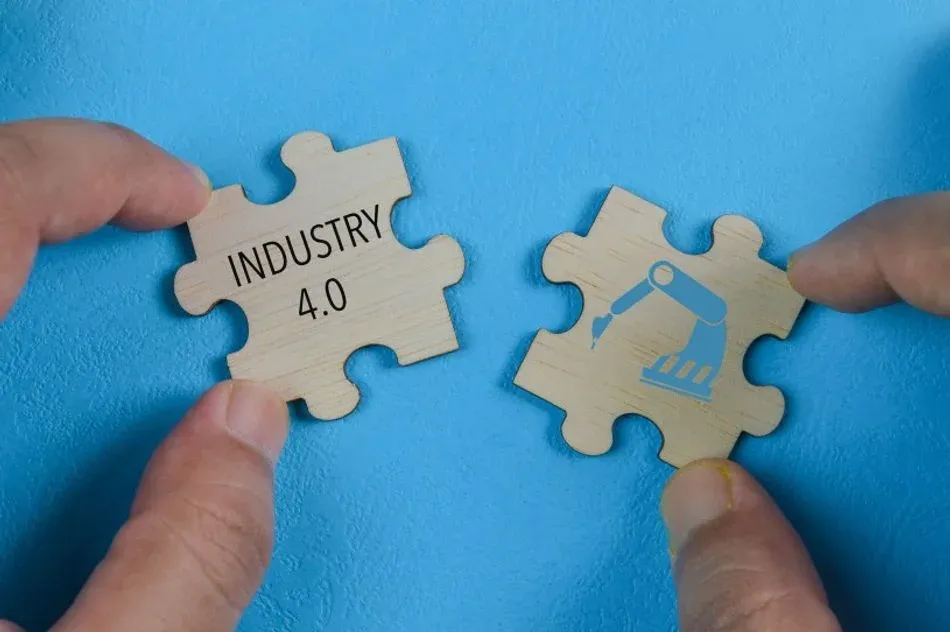
Factors to consider when choosing ERP System for metal fabrication
One of the major factors in choosing an ERP is its pricing. It must be in line with the budget allotted for the purchase and set-up costs. Another factor to consider is whether it is flexible enough to accommodate changing requirements in business operations. Being able to customize your experience can be vital in this regard.
The software should also be easy to learn and use, or else it will only add to the existing office and production bottlenecks. Finally, make sure that accurate data flows unhindered through all stages of your company. If the software is very compartmentalized into separated software modules/databases, it will probably be hard to create a good collaboration in your business.
Tip: Any good ERP-software maker should let you try out their solutions, whether on a demo instance or a trial account. This is important because you need to experience how the flow of the system is and if it works right out of the box. A lot of customization up front is usually a red flag.
Cloud, Hybrid Cloud or Native Cloud?
With the advent of digitalization, more and more companies are moving their data to the cloud. But, there are many benefits and drawbacks of both types of cloud.
- On-premise solution: Installed on PCs and connected to a server in your business. Usually, a robust solution, but requires server specifications and maintenance. Can be complicated with multi-factory or multi-site solutions.
- Hybrid Cloud: Installed on PCs and connected to a server hosted by the vendor (externally). Commonly used for multi-factory solutions, less recommended for single-factory solutions. Performance is often slower than On-premise.
- Cloud (Native): No installations necessary, software is running from your web browser. Can be used by single and multi-factory solutions, and often has exceptional performance when designed well. Typically, requires on-premise integrations with other software such as CAM, MES, and CAD.
Integrations and app exchanges
It's not common for your company to only work with ERP software; there is typically CAD, CAM, and MES software in your business. It has been shown repeatedly that integrating such solutions is crucial for the long term success of your implementation.
In our selection, we therefore look for systems that are easy to integrate. The easiest way to do this is if the vendor provides an API and an app exchange. Below are a few selection criteria you could consider.
To make integrations easier, look for :
- Are there off-the-shelf integrations for your software systems?
- Is there an API that is well documented?
- Does the company provide an app store?
- Does the company have a proven track record in your industry?
- Do they provide their own consulting, or are you dependent on third parties?
What integrations do you usually need?
Common integrations needed:
- CAM-integration, for example, the programming software of your machine
- MES-integration, for example, your machine job manager
- CAD-integration, for example: SolidWorks, Inventor, CATIA, etc.
Tip: Ensure you speak to your vendor about API-connectivity and the cost of this, so you can easily connect other apps or built your own. While not necessary, some great bonus features of great connectivity are the ability to import CSV, XML and JSON files, so you can import customer orders directly in your system.
Regional / local support
Can your software providers comply with your local and customer regulations and quality requirements for quality and security purposes? For example, think about data protection (GDPR), but also quality standards such as ISO 9001.
It's not uncommon that countries or even states have vastly different requirements. If the software company does not have insight into the local requirements, you might be up for disappointment.
It is important to always be mindful of the safety concerns involved when it comes to selecting computer software. The best way to ensure you are playing it safe is by seeking a partner network that is global and trusted, and hiring a specialized third party with knowledge on the latest advances in technology.
Tip: Make sure your vendor has a 24-hour support service, so you can always reach them in case of an issue. Whether you're working through a reseller or directly with the provider, you must make sure that your system comes with good personal service.
Do they understand your shop?
Many software solutions are not designed in workshops, but are instead designed by financial departments or for large enterprises. This can create friction when your daily smart work methods are not there from the start. Especially when you consider metal fabrication to be such a specialized industry.
Changing a generic product for a customized one is usually an expensive undertaking that most manufacturers and fabricators can't afford.
Therefore, it makes sense to question whether the product has been developed at, by, or in collaboration with your industry.
In case you're choosing a generic product, make sure that there are specialized partners and providers for your industry. In the comparison below, we will pay extra attention to this factor.
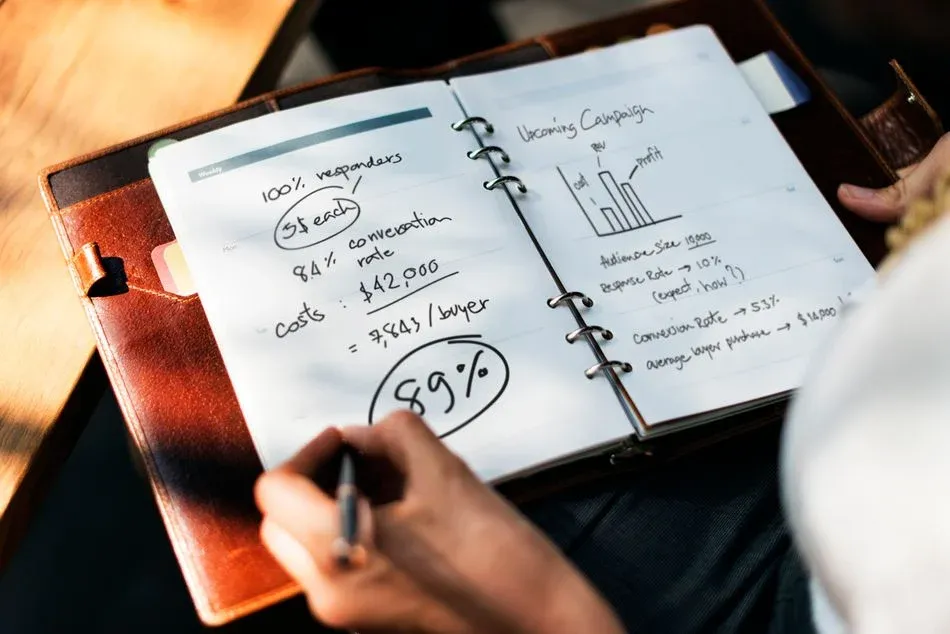
Quick Guide to 10 Best ERP Systems in the Market
Today, there are many ERP software solutions available in the market. It’s challenging to make an informed decision. In this article, we have compiled a list of 10 best ERP solutions you should take a look at.
The 10 Best Metal Fabrication Software Systems
Bemet (ECI Software Europe)
Overview:
Bemet is specifically designed for the metalworking and metal fabrication industries, offering robust ERP functionalities that cater to specialized manufacturing processes.
Product Information: Bemet
Business Central (Microsoft)
Overview:
Microsoft Dynamics 365 Business Central is a comprehensive, cloud-based ERP solution that automates and connects business processes across sales, purchasing, operations, accounting, and inventory management for small to medium-sized businesses.
Product Information: Business Central
BySoft Business (Kurago Software)
Overview:
BySoft Business is not an ERP but a best practice add-on for Microsoft Dynamics 365 Business Central, designed to enhance efficiency in the metal fabrication sector by integrating specialized operational processes.
Product Information: BySoft Business
Fulcrum Cloud
Overview:
Fulcrum Cloud is a newer cloud-based manufacturing app, providing tailored ERP solutions for project-based manufacturers looking to streamline operations and manage projects more effectively.
Product Information: Fulcrum Cloud
Genius ERP
Overview:
Genius ERP is tailored for custom manufacturers in the metal fabrication industry, focusing on optimizing operations, inventory management, and production scheduling.
Product Information: Genius ERP
Infor M3
Overview:
Infor M3 offers extensive ERP functionalities for medium to large global manufacturers, supporting complex manufacturing, financials, and supply chain management.
Product Information: Infor M3
JobBOSS² (ECI Software Solutions)
Overview:
JobBOSS² provides essential tools for small to medium-sized custom and mixed-mode manufacturers, including job quoting, scheduling, and real-time job tracking.
Product Information: JobBOSS²
Odoo
Overview:
Odoo is an open-source ERP offering a suite of business applications that cover a broad spectrum of enterprise management needs for businesses of all sizes.
Product Information: Odoo
Priority ERP (Priority Software)
Overview:
Priority ERP provides flexible, configurable ERP solutions that are easy to adapt for mid-sized businesses, covering manufacturing, HR, CRM, and financials.
Product Information: Priority ERP
Ridder iQ (ECI Software Europe)
Overview:
Ridder iQ specializes in ERP solutions for small to medium-sized discrete manufacturers, enhancing efficiency through advanced manufacturing, inventory, and CRM capabilities.
Product Information: Ridder iQ
These entries now offer a comprehensive overview of each ERP software and add-on, formatted to provide quick access to key information and links for further exploration.
Conclusion: Pick an ERP-Software that Fits Your Needs and Budget
It can be difficult to figure out the best ERP system for your company. There are many different systems on the market, and it can be difficult to choose which one will work best for you.
You can’t achieve the maximum benefit of an ERP without a number of different systems working together.
This includes ERP, CAM, MES, CRM, and BI tools. Every software package has its strengths and weaknesses. As such, it is important to get an idea of what your business needs before deciding on your digital transformation journey.
Choosing the wrong ERP system for your company can have a huge impact on your production quality - from increase lead times, to lower accuracy in resource scheduling, to a lower level of customer satisfaction.
Don’t try to reinvent the wheel by yourself
We help companies around the world with independent advice in English, Dutch, and German. Get in touch today for your first free of charge call.