Have you ever tried to run your business more efficiently?
If so, you'll know that it's difficult because there are many ways to do this. Maybe you've looked into LEAN processes, or considered buying more machines, but in most cases, you're out to focus on metal fabrication ERP software.
So, what do you do? Many metal fabricators have found success by using modern ERP.
But there are a few things you should know before you buy and implement a new ERP for metal fabrication to ensure that you will be able to streamline your operations and make your processes safer, without the common frustrations that might come with such a project.
This post will explain the key points to consider when choosing an ERP that will allow you to successfully increase your business output without spending too much money.
Why Enterprise Resource Planning (ERP) is important for metal fabrication?
If you work in the metal fabrication industry, you're in a highly competitive business where price and speed are key factors to be a relevant supplier for your customers.
ERP has grown to be an indispensable tool for manufacturing companies, and many metal fabricators are now relying on their ERP systems to run the daily business to a large extent.
A good software solution will help you streamline operations and make processes faster, more reliable, and give you a better overview of how things are going. It will help you eliminate many repetitive manual tasks, and it will create a central source of truth where you and your entire team can rely on.
Instead of having post-its on computer monitors everywhere, stacks of papers on desks, and people running around the shop asking questions, a good system will allow you to integrate all this βtribal knowledgeβ into one reliable system.
Metal fabrication is a complex process that involves purchasing, planning, production quality, and more. As a result, most manufacturing companies rely on specialized systems to streamline operations and make their processes safer.
It doesn't matter if you have years of experience under your belt or are just starting out and intend to be involved in the metal fabrication industry, you should definitely consider investing in more than just the tools and equipment you need on the job site.
If you are already working with ERP, but are unsure if you should upgrade to the newest generation, for example, to switch to a cloud-based solution, also read on.
What is enterprise resource planning (ERP)
ERP is a software system designed to help organizations manage their resources. The latest versions are used to organize information from different departments in one place, making it easier for organizations to make decisions and act quickly.
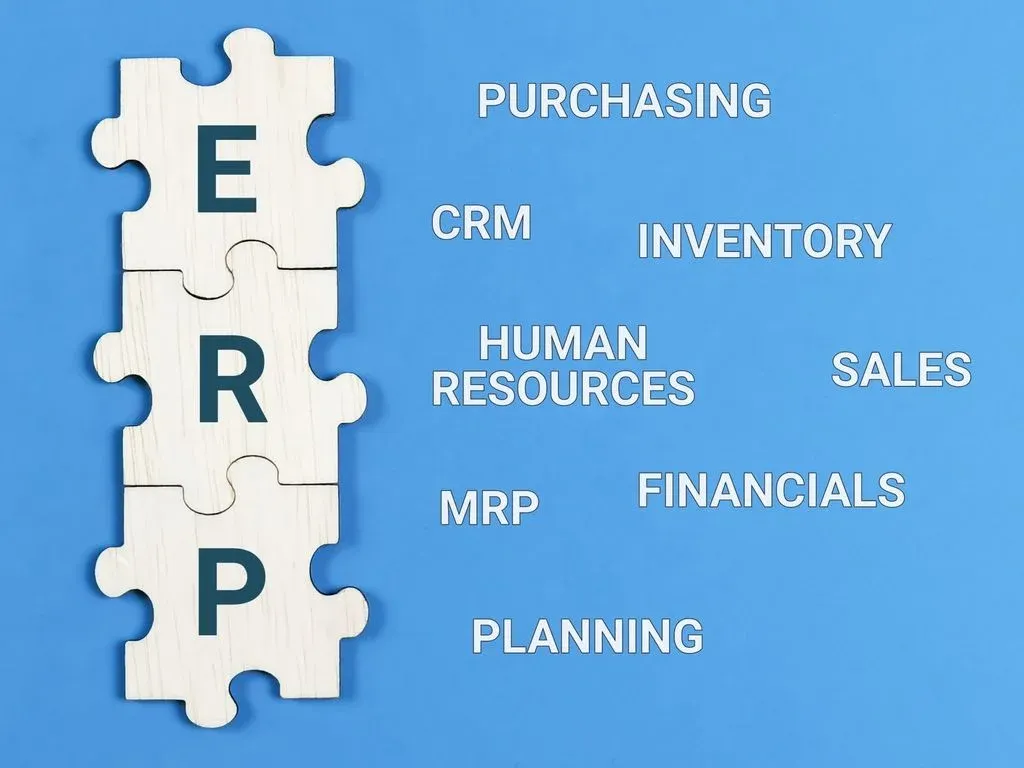
A reliable metal fabrication ERP helps businesses focus on their core competencies by providing a centralized platform for managing all aspects of a company's operations. This includes supply chain management, customer relationship management, project portfolio management, and workforce planning β all in one integrated solution.
History of enterprise resource planning (ERP)
Even though understanding ERP is a little confusing, it is good to understand it for all businesses, especially the manufacturing industry. Because software has its roots in the manufacturing sector, itβs not surprising to see that itβs at the core of many businesses today.
In the early 1960s, the first computerized systems were developed to manage inventory, to manage, monitor, and get some basic reporting about the current inventory balances. This led to a later expansion in the form of Material Requirement Planning (MRP). This included the first forms of planning, where the systems could generate production requirements for finished goods.
Later in the 1980s, the rise of the next stage started: Manufacturing Resource Planning (MRP II), which now also included product planning, parts purchasing, and product distribution. This was the launch of the new era, where computer systems replaced mostly manual production planning back in the day.
The 1990s was the start of Enterprise Resource Planning (ERP) as we know it now: an integrated system that includes many business functions. The goal was to achieve control and overview of the business where Money, Material, Manpower, Machinery, Marketing, and Methods could be integrated.
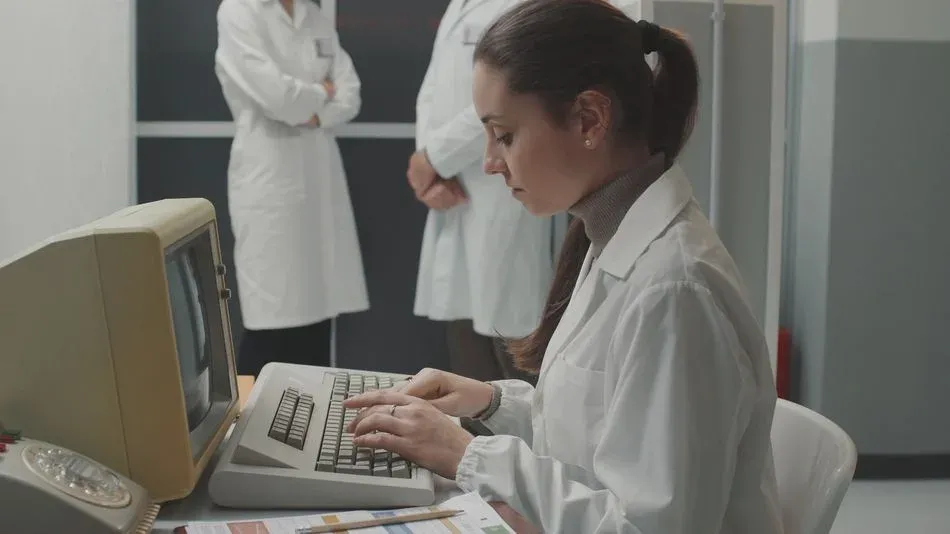
Until the early 2000s, many smaller businesses were unable to afford a system like this. Fast-forward to the 2010s and beyond, and many small businesses can now also effectively utilize the power of modern business software.
The latest developments of this business software include interactions with other application suites and accessing information via internet web-browsers and mobile devices. The second major development is cloud-based ERP, which delivers business applications as a software-as-a-service (SaaS) model.
In short, ERP-systems have evolved to meet the needs of larger players in the manufacturing industry. Now they are vital for all types of businesses with their broad, flexible features. Small, medium, and enterprise industries require modern software systems to get centralized, real-time data.
Metal fabrication companies need ERP to run efficiently
If you look at the history of the development, it's no surprise that metal fabrication companies require ERP to run efficiently. They need to work on inventory, accounting, production planning and scheduling, delivery schedules, material procurement, and transportation management. Without such systems, these tasks would be extremely difficult to manage.
Surprisingly, there are still many companies that work with loose systems or even Excel. This might work when your company is small, but as soon as your responsibilities grow, it becomes an impossible task to maintain all these systems without proper integration.
The actual cost of a project can vary hugely from one project to another, so if you're going to be spending time at a job site, making sure your materials are being tracked and managed is crucial.
Successful metal fabrication companies often have the right systems in place so that they can be trusted, and it doesn't all depend on the CEO, owner, plant manager, or people who have to remember things. As we've seen in the past few years, it can be quite dangerous if some staff members unexpectedly can't show up at the office and business must continue.
What are the benefits?
- ERP-systems provide a one-stop shop that is useful for coordinating all the different parts of a business, making it easier to track products, cost, inventory, etc.
- A good system tailored to metal fabricators can significantly increase productivity, enhance efficiency, improve quality control and shorten lead times.
- Further down, from a managerial perspective: It helps you make better financial decisions, better track data, access information quickly and accurately, and make it easier to improve processes and decrease errors.
- This is achieved by reducing manual activities that are necessary to prepare production orders and ensuring you're in full control of your operations and planning.
What are the drawbacks?
The most common issue is that many manufacturers still use legacy solutions, which are costly to maintain and unfriendly to users. For example, if a system is designed for legacy versions of Windows, it might hold back the entire company to comply with latest IT-standards (and resulting security risks). Legacy software is usually not built on modern databases or in the cloud, which can severely limit opportunities for integration.
On the other hand, there is a new generation of software in the market. This does not mean that all issues are solved and that there are one-fits-all solutions for sale. If you want to succeed in the fourth industrial revolution, a good solution must be tailored to your processes.
Hereβs why:
Modern software is well-designed, but often causes issues for organizations when executed poorly. The biggest drawback is the lack of expertise in the field that covers both best practices in metal fabrication and designing modern IT-systems and infrastructure.
Other common mentioned drawbacks are that they are typically difficult to implement, expensive to maintain, and require constant updating. Moreover, they are hard to use for less-technical people in the company.
Especially for the metal fabrication market, which is highly varied and interconnected, selecting the right system is challenging. The last but not least drawback is the total cost of ownership. Legacy software is usually sold at a base price and supplemented with lots of additional consulting, which can lead to costs 3-5x the investment of the software.
On the other hand, there are new cloud providers with fixed monthly costs and limited consulting, but monthly costs over the course of many years should always be considered, since year over year expenses can spiral out of control quickly if there is no oversight on this.
What to look for when choosing an ERP solution?
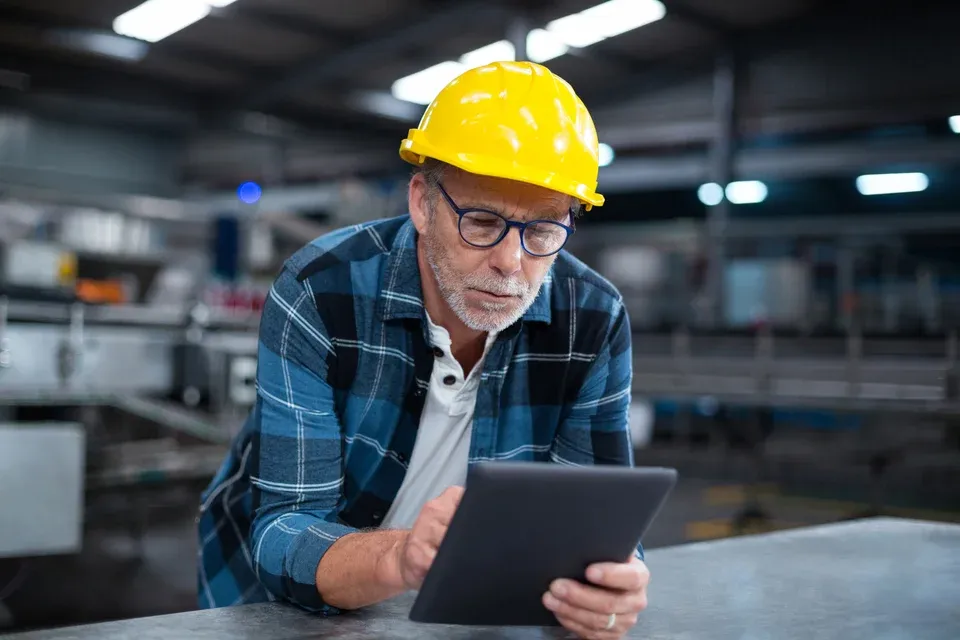
If you're looking for a new business software for your metal fabrication business, the best way to ensure you end up with something that lets you run all your important processes is by looking for these things:
- Make sure your ERP-system lets you integrate with your other apps, such as CAM, CAD, and MES. If it doesn't, you'll have trouble because you'll have to manually type over data from one system to the other.
- Ensure your ERP software has an API or open XML interface, so you can connect and create your own external apps and easily import and export data to your system.
- Any good software will be supported and developed for years to come. The manufacturing industry changes rapidly, and keeping up with the latest standards, file formats, and regulations will be crucial to keep the competitive advantage.
While not necessary, some great bonus features of a great ERP are built-in CRM functionalities and a remote support team, so you'll be able to receive help remotely without having to wait for consultants to visit your shop.
You might expect that a cloud-based solution is also on hard requirement these days. This might be true in numerous instances. However, there are plenty of fields where ERP does not need to be in the cloud. As long as it can integrate with the cloud (open standards), there is usually no need to make the switch yet.
Using a cloud-based system
Advantages
- The system provides remote access
- Applications are scalable
Disadvantages
- Dependent on cloud availability
The advantages of using a cloud-based system
One of the top advantages is that it is accessible from anywhere. This means that you can have access to your company's data from any location, including your computer at home or on the go with your mobile device. In addition, these applications are scalable, meaning that they grow with your business without much additional expense or effort.
The disadvantages of using a cloud-based system
Because the software can be completely hosted in the cloud, there's a chance you might not reach the cloud on a given moment. Although this happens less and less, itβs still a relevant risk. Additionally, the maturity of many ERP systems might be inferior to on-premise systems, which often have more than a decade of experience under their belts.
Now that you know what to look for in metal fabrication ERP, you're ready to start digitizing your processes without worrying that you might select a solution that doesn't work for your business.
How to implement ERP in your business
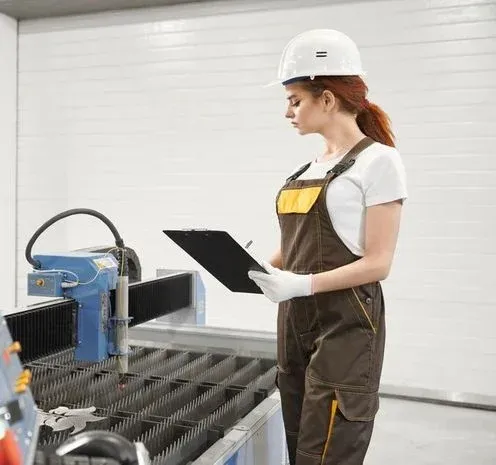
The implementation of an ERP-system can be a long, complicated process. It is vital to establish the needs of the business and how the software will cater to those needs. Before you implement the system, it's important to map out all your processes, so you know what to focus on once the software is in place.
This can be done by a blueprint, which is frequently accompanied by an effective change management plan (and selecting the right partner who should be helping you implement it).
A blueprint describes the current and future business processes. The plan should include timelines, milestones, and resources that are needed for the migration. The most significant argument is that hidden ERP implementation costs or failed projects can be prevented because the requirements are clear.
The problem with ERP implementation is that the requirements are often not clear enough. The lack of clarity will lead to hidden implementation costs and even failed projects. For example, which database holds which information and what adjustments might be necessary to make the process work for your business. Also, not to forget are necessary ERP-integration, for example with CAM, MES, and CAD.
A change management plan is the process of ensuring that employees are on board with new changes and that all other stakeholders are adequately prepared for the change.
Only after the system is designed and tested is it time to start migrating your existing data to your new ERP system. The process of migrating data from old columns to new ones can be tedious. It is important to create a plan for the migration before the process begins.